The realities and challenges we face attracting and retaining great staff.
With the COVID-19 threat receding and society returning to some form of normalcy, workshops across the country have enjoyed a resurgence in business, in many cases exceeding pre-pandemic levels. This is welcome news for workshops, however, also brings back into focus a huge issue for the industry – attracting and retaining qualified staff.
To better understand the challenges, we need to take stock, raise the hard truths, look at the data and develop plans to tackle this issue head on.
Attracting and retaining staff, both apprentices and fully qualified, is the single biggest issue for more than half of Australian workshops, and the data supports this. Workshops are advertising for staff, but have few applicants. Due to the slim pickings, finding a candidate with the right attitude and skills is proving hard. The resultant lack of staff has led to 30 per cent of workshops turning away customers, and this stunts business growth.
What are the challenges that have been driving these realities? The AAAA 2020/21 Workshop Employment Insights conducted by ACA Research offers some important insights about what is working and not working in relation to staff and retention.
Let’s start with the elephant in the room. Wages. There is no denying that on the whole, mechanics are paid less than other trades. This can undoubtedly stifle interest in pursuing an automotive career before it has even begun.
Looking at our worker mix provides another clue. Currently less than 2 per cent of automotive technicians are female. Are we only talking to 50 per cent of the population about careers in automotive?
The age of the workforce can’t be swept under the carpet either. Across the board, 67 per cent of qualified mechanics are now aged over 50 years old. Are we doing enough to foster the next generation into this rewarding and driven industry? Is an automotive technician seen as an attractive career choice?
The bottom line is we aren’t getting enough apprentices into the industry, and this needs to be addressed.
Workshops are also having a hard time retaining apprentices. For owners and managers of workshops, hiring an apprentice is a significant investment in time and resources. Having an apprentice drop out, or move elsewhere is a significant blow and disincentives workshops to continue to hire apprentices.
Addressing these issues and effecting change is tough, there is no denying that. And there is no silver bullet here. Change needs to come from all levels. In the workshops, in our schools, at the vocational training level, with government and even more broadly in society, around cultural norms.
What are some proactive steps workshops can take? With the job market currently skewed towards being an ‘employee market’, what we are seeing from the data is that qualified mechanics are picking and choosing where they work based on the salary, the conditions and the workshop environment. The hard truth is that 61 per cent of recruited staff are moving from another workshop. Are they moving from yours?
Workshop owners and managers should be asking, ‘what am I doing to retain staff?’ and ‘is my offering competitive’? Paying above award wages is a part of this package, but it is far from being the only consideration in play. 84 per cent of leading workshops, who do face less staffing issues, are paying for the training and upskilling of their staff, and 60 per cent of these workshops provide career progression.
Granted, career progression is not realistic for many smaller businesses, but even smaller strategies can have an impact on staff retention. Everything from paying for a social event to help team morale, providing flexible hours, mentoring, or even making improvements to the work environment itself.
It comes as no surprise that over 80 per cent of workshops feel the government should be doing more to grow the number of qualified mechanics in Australia. How the government will achieve this is complex, but needs to take into account the current pathways – from primary to secondary school, through to vocational training institutes. Changing views around the perception of automotive being a career for men should also be actioned.
How can industry bodies like the AAAA play a role in effecting change? Its research findings are a great tool to better understand the challenges of our industry and provide insights to government.
It also needs to continue to advocate for further support in funding toward increasing vocational careers, in particular automotive technicians, and better understand why such a high percentage of apprentices are starting but not completing their qualification.
“Although as an industry we have to face some difficult truths, I remain optimistic,” Australian Automotive Aftermarket Association CEO, Stuart Charity said.
“As technology increases its role in automotive repair, I am buoyed by the fact we will soon have a mandatory data sharing law in place. This will ensure workshops are future proofed against these advances and can continue to offer their important services that keep Australia moving.
“New technology also presents an exciting new opportunity to attract younger generations into the industry.
“Finally, the AAAA will continue its role pushing for change and supporting the industry and our members so this vibrant and rewarding career remains a job of the future.”
For more detailed content on the automotive aftermarket industry visit, www.aaaa.com.au.
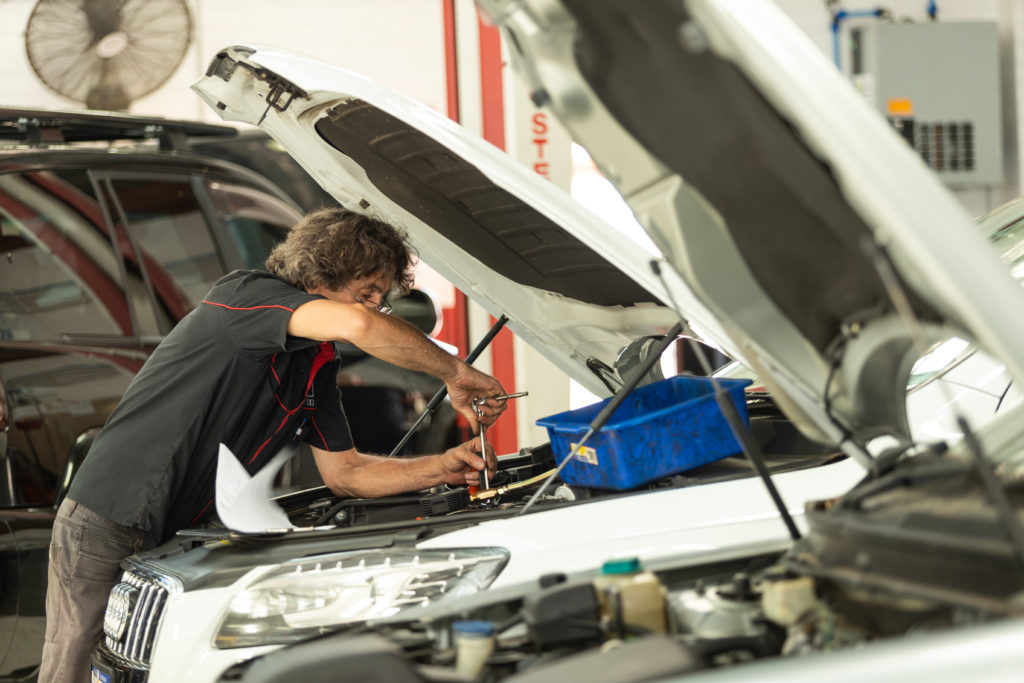